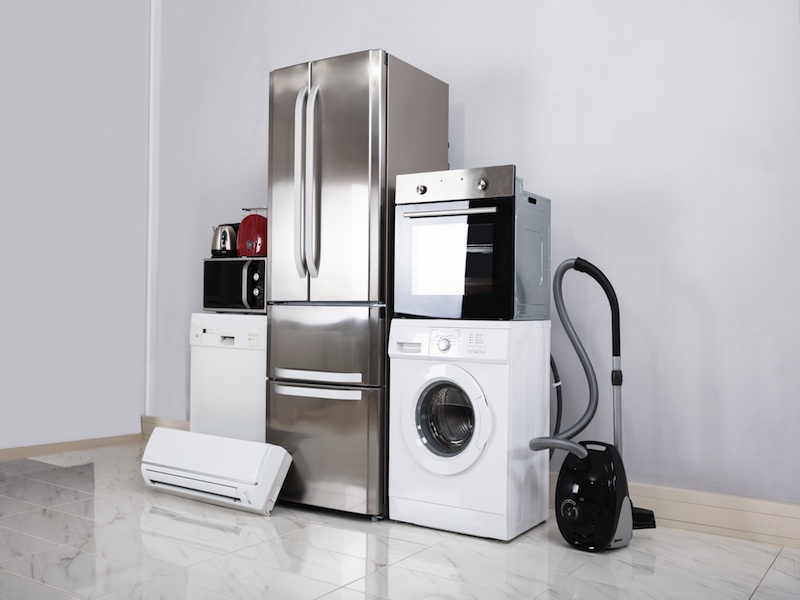
NAPIT Technical Development Engineer, Richard Townsend, discusses some of the issues the electrical installation industry seems to be facing when it comes down to cables covered by thermal insulation.
Given the constant drive to save energy, reduce energy bills and limit heat loss from a domestic dwelling, the use of government-backed and funded schemes to upgrade existing properties is widespread. The most common of these is to install large amounts of thermal insulation in the loft of older dwellings, as well as new build properties. On paper, this works very well, but there are some issues that the electrical installation industry seems to be encountering.
It’s always been known that cables buried in thermal insulating material, will reduce their ability to dissipate heat, meaning they’ll reach their optimum operating temperature with less load applied. The amount of load required to require a reduction in the current-carrying capacity of a cable, before it reaches its operating temperature, is dependent on a few factors:
1. The U value of the insulation
2. The depth or amount of any insulation
3. The duration of loads expected
4. The general expectation of constant loads
U value and insulation depth correlation
Basically, the U value is the rate of loss of heat through a building material or component, which is usually given as the amount of Watts per square metre, per degree of temperature (Kelvin).
U = W/m2K
The lower the U rating, the less energy loss, the more efficient the insulation.
The higher the U rating, the higher the energy loss, the less efficient the insulation.
The depth of the insulation is also important as this will affect the U rating because not all insulation is the same.
The U rating has been lowered over the years, and insulation has suited to match the lower requirements; therefore, some older thermal insulation may well be higher than more modern equivalents, and some modern thermal insulation types can vary wildly.
BS 7671 Reference Methods 100 and 101 mentions U values of 0.1 W/m2K, this is a very low figure and refers to the building or section of a building as a whole, which is taken from the requirements of Building Regulations, which take account of all of the thermal barriers. Even some of the most efficient thermal insulation placed between joists can only manage 0.335 W/m2K with 150 mm depth coverage.
We must understand that the 100 mm figure given in these two reference methods, also refers to an equivalent overall building value of 0.1 W/m2K for 100 mm. This is very misleading as it leads people to believe that 100 mm of insulation can meet the 0.1 value, which is impossible, as nothing that efficient currently exists within the market place. This means that older thermal insulation may need to have well in excess of 100 mm to meet the same equivalent of 0.1 W/m2K for 100 mm.
Thermal Insulation is generally advertised with values of thermal conductivity and/or resistance, which appear similar to a U value and given as W/m K. This isn’t to be confused with the U value, which is a factor of the entire building and given in W/m2K.
Load duration
The duration of any expected loads also has an impact. Short duration loads may not generate the heat build-up required to damage the insulation of conductors in a cable, such as an electric shower. Constant loads are likely to be more of an issue, as these can increase the cable temperature over time and cause cable insulation breakdown.
The most affected circuits tend to be 2.5 mm2 ring final circuits (RFCs), shower radials, and heating circuits (including immersion heaters). Lighting circuits and similar are generally wired in 1.0/1.5 mm2 cables and protected by 6-10 A overcurrent protective devices (OCPDs).
These types of circuits can happily run at their design capacity in thermal insulation, due to their inherent spare current carrying capacity afforded by the cable and the low rating on the OCPDs.
That said, we need to also evaluate the load requirements for the modern domestic property, the RFC was first derived after the WWII, and space heating appliances in properties were common; central heating as we know it today, wasn’t available.
The expectation of constant or high loads
The modern property doesn’t require its RFC to carry large loads; indeed, most standard properties will struggle to consume more than 25 A in total, with all appliances switched on (an electric shower isn’t used in this measurement).
All the electrical equipment we use today is energy efficient. TVs, washing machines, ovens using smart heating programs, tumble dryers, vacuum cleaners, LED lighting, etc. are all far more efficient than could have ever been dreamed of when the RFC was introduced, and they’re still improving and using less energy.
Its for these reasons a 2.5 mm2 RFC in thermal insulation is unlikely to reach a point that will cause it to overheat or be damaged, and we simply don’t put that amount of demand on them in a modern environment.
Electrical Installation Condition Reports (EICRs)
If during an EICR, an inspector needs to evaluate the insulation, where it is not part of an agreed limitation with the client, they must find out what type and U rating equivalent the thermal insulation is. This can be difficult and may not be practicable. For RFCs, it’s
unlikely this will be a problem.
In a privately-owned property, inspections tend to be at low frequencies, or at their sale, after which the installation is unlikely to be inspected again for some time, if ever. In these cases, the inspector should code cautiously as, over time, the life expectancy of short-duration high loads, electric showers, etc, may shorten the lifecycle of the cable.
The inspector may choose to code this a C2 or increase the frequency of recommended inspections to check the cable condition and give a C3. If there are any signs of thermal damage, or the cable insulation is showing signs of heat damage (drying or becoming brittle) then a C2 should be used.
If an inspector is carrying out EICRs in social housing or private rented sector properties, the frequencies of inspections are likely to be high; certainly no more than five years, and maybe less if there is a change of tenant. For this reason its unlikely that either RFCs or shower circuits in thermal insulation will cause a problem as they can be effectively monitored before the cable life expectancy is reduced. A C3 is acceptable in these cases.
If a housing authority requires further monitoring, they have the option of taking a percentage of their stock (10%, for example) and monitoring the energy usage (load). This will also help to identify the likelihood of cable damage. This information can be used to evaluate all stock and make changes if/when they’re needed. Electronic software can also be used to track EICR findings and highlight suspected cable damage and lifetime reductions before they cause an issue.
When we talk about cable life expectancy, we refer to a manufacturer’s effective lifecycle of its cable; different manufacturers have different views, but generally 35 years + isn’t likely to be a problem. When cables are subjected to overload, heat, or other external influences, their life expectancy, or useful shelf life, may be reduced.
The reduction varies with the level of overheating etc. and may only be a few years less than its expected usefulness. The only way to monitor this is through regular inspections. The social housing sector generally does this adequately and need only instruct their inspectors to check for signs of thermal damage, in order to monitor the need for any remedial actions.
Conclusion
To recap, with frequent monitoring for signs of degradation, where cables are covered by thermal insulation, efficient enough to impede BS 7671 Reference Method 101, a C3 is considered to be adequate.
Where frequencies are low or non-existent, cables impeded by thermal insulation may be given a C2 or C3 if a future frequency is reduced (generally for the private rented or homeowner sector).
Where the thermal insulation value, and how it affects the whole building insulation, is not known, and therefore an infringement of Reference Method 101 can’t be confirmed, an FI code could be considered, but realistically, without evidence of any thermal damage, a C3 would be more appropriate.
Where thermal damage or degradation of the cable insulation is evident, a C2 should always be given.
Get more details about NAPIT membership by clicking here