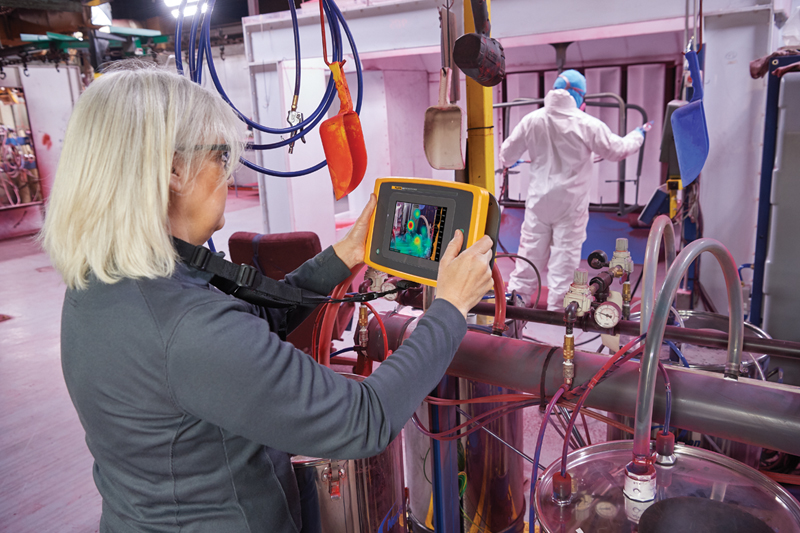
Is it time to consign listening and bubble watching to the history books when it comes to detecting air leaks in a busy factory? Mark Bakker, Field Application Engineer at Fluke, discusses.
Believe it or not, in the 21st century there are still engineers tasked with listening out for the hissing sound of air leaks in noisy factories while others pour liquid on suspect piping and look for air bubbles to appear… much like looking for a puncture in a bicycleβs inner tube. A major difference, of course, is that many holes in a large factoryβs compressed air systems are invisible to the human eye (and ear) and are almost impossible to locate using these methods.
With the British Compressed Air Society (BCAS) estimating that as much as 50% of compressed air in a factory can be lost through leakage, engineers are spending huge amounts of time searching for leaks. At the same time, manufacturers are wasting enormous levels of energy β itβs reckoned that UK factories use 10TWh of energy annually to create compressed air β while compromising significantly on productivity and output.
Of course, there are many thousands of engineers who no longer rely on their ears and eyes to detect leaks and have turned to ultrasonic equipment that is less affected by noisy environments.
A sound investment?
Ultrasound scanning is certainly an improvement but unless you know where a leak is in the first place, some kits can struggle to find it and engineers essentially have to scan and hope for the best. Even when a signal is picked up that signifies a leak, pinning down its exact location can be extremely difficult. In addition, readings from ultrasonic scanners can be impacted by electronic interference that can result in them being unreliable and misleading.
For factories keen to identify, locate and fix compressed air system leaks as quickly and efficiently as possible, boosting productivity and slashing energy overheads in the process, acoustic imaging represents the best option available to engineers looking to cut air losses down to as little as 5%.
One solution to this need is Flukeβs ii900 Industrial Acoustic Imager. Rugged and ergonomically designed, this hand-held device weighs 1.7kg and incorporates a 7β LCD display with backlight. Users can literally see leaks on the screen via a βSoundMapβ. Even with limited experience, operators can detect air leaks quickly in noisy environments and from a safe distance, thanks to 64 digital microphones built into the unit.
Leak volume and cost indication can be measured accurately while on the go and even CO2 emission reports can be generated by the ii900. With 20Gb of storage capacity, users can save readings as JPEG or PNG images or as MP4 videos. Data is gathered using Flukeβs LeakQ mode, designed specifically for capturing and analysing leak data to determine the size and type of leak β for example, quick disconnect, threaded coupling, hose or open end.
With an acoustic imager, factory owners can expect not only to cut energy costs and increase efficiency but also protect expensive equipment which can be at risk of serious damage through system pressure being too low or too high.
Visit the Fluke ii900 Industrial Acoustic Imager product information page online here