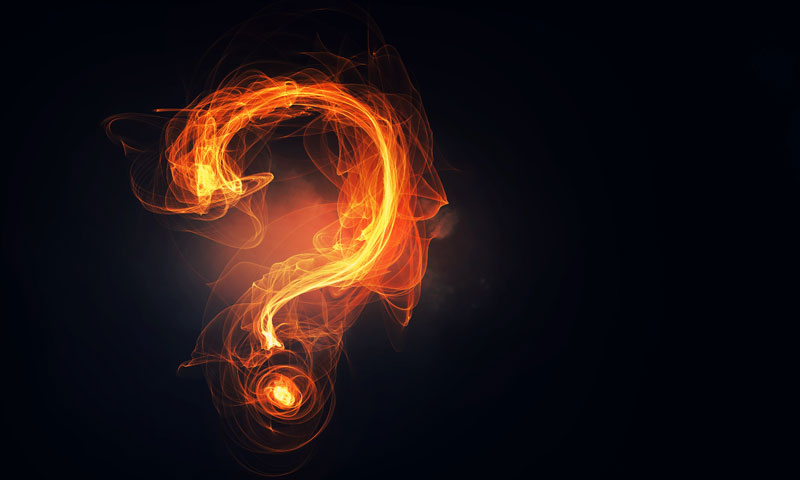
We’ve talked about emergency lighting, but what about the other safety lighting requirements, such as fire rated downlights? Phil Knight (MIFireE), Exemplar Fire Safety Consultancy, answers some key questions.
What’s the purpose of a fire rated downlight?
The purpose of the fire rated lighting unit is to ensure that no weak spots are created in the FR ceiling, thereby helping to ensure the integrity of the structure is maintained in all areas.
When/where should fire-rated downlights be fitted?
Fire rated downlighters must be installed into any partition (usually a ceiling) that must meet fire resisting (FR) standard, i.e. the requirements of the relevant part of BS 476. Most often, designers will specify downlighters to be installed (for example) along a corridor that constitutes a protected means of escape, therefore the lighting unit must be fire rated to the same level as the structure into which its fitted. In practice, most ceilings that form part of the structural floor above must be to an effective FR standard. However, where false ceilings are installed below the structural floor (in an open plan office, for example), then FR rated light units aren’t required unless (in rare cases) the false ceiling also needs to be of a FR standard.
Where does responsibility lie in the fitment of downlights?
In these days of self-regulation and risk assessment, responsibility and liability can be a complicated area. Much will depend on the design specification requirements of the building. For example, if the designers haven’t specified FR down lighters to a ceiling required to be FR, and the installer fits exactly as shown in the specification, then the installer shouldn’t be deemed to be liable in the event of an incident or regulatory inspection.
However, where the design brief is to fit FR rated light units and the installer goes against that specification, then the installer is more than likely to be held at least partly responsible. I say ‘partly responsible’ because many projects will be subject to checking and inspection at various levels or stages throughout the job. Where such a regime is supposed to be in place, at least part of the responsibility should be upon the inspectors.
Smaller projects may have no detailed light fitting specification or be subject to an inspection regime. In these cases an electrical engineer or fitter who pays no regard to FR light units is likely to be the person most responsible.
How is downlight quality and effectiveness usually tested?
Where a light unit is required to be FR rated, a responsible manufacturer will seek to have their products designed and constructed so to meet the test criteria in order for it to pass stringent live fire tests. These tests are (usually) set by the British Standards Organisation and/or equivalent European tests. Samples of the unit are sent to independent test laboratories where they’re subject to thorough and controlled live fire tests. The results are recorded and reports sent to the manufacturer or sponsor of the tests. If satisfactory, the unit is deemed to have ‘passed’ and certificates are issued by the organisation carrying out the test.
In addition, the responsible manufacturer will not only ensure rigorous standards are maintained throughout production but will also ensure that the finished product will be subject to batch testing; the more professional companies may even have their own in-house testing laboratories.
Will it be possible to incorporate new designs in downlights without compromising the effectiveness of the product?
There are products currently in development that don’t incorporate a traditional can but have passed the required rigorous testing and are FR certificated. These units with no can are likely to be smaller, lighter and sleeker in design, whilst still retaining the FR rating.
An Evolution of Fire Rated LED
In a recent example of the new wave of radical new designs entering the lighting market, Integral LED has opted to overhaul the conventional design of the fire-rated downlight – one of the ‘toolbox essentials’ used by electrical contractors everywhere.
Utilising the benefits of LED, the new Evofire range has dispensed with the need for a metal can, in a major re-engineering of a familiar fitting. Instead the Integral Evofire has adopted a novel approach of creating a glass and steel barrier as a solution, meaning that the fire protection is, essentially, deployed below the lamp at the ceiling surface.
The resulting lightweight downlight is rated BS 476 and matches current fire regulations. However, the new product goes beyond this to provide an effective barrier to smoke and flames entering the ceiling void – extending the escape time in the instance of an emergency.
The Evofire’s open design allows the separately fitted LED spotlights to breathe freely. Under test conditions, the interchangeable GU10 and MR16 LED lamps have shown to run up to 10°C cooler than a typical model using a can. This critical lower temperature provides a major boost to LED longevity, potentially doubling the operational lifetime of the LED unit.
A built-in insulation guard variant of the Evofire also ensures ‘cool’ operation, even when insulation material is laid above the downlight fitting. Hence, heat efficiency of the building can be maintained without compromising lamp-life.
The Evofire downlight is made from highly durable steel and fits a 70mm cut-out. The bezel has a high-quality finish and is super-slim with a remarkably thin profile of only 1mm, so it can blend in and look great in any ceiling.
Additionally, a premium model is targeted at highly designed interiors with a 20mm recessed design and an in vogue trimless version for a seamless look. The radical new design has been tested by a UKAS accredited fire laboratory for 30/60/90 minutes in a full furnace.